Lame MU#
Lame MU = {model_name} {float_list} [M/ :math:`Lt^2`]
Description / Usage#
This required card is used to specify the model for the Lame coefficient μ for the solid constitutive equation (see Sackinger, et. al. 1995, and Solid Constitutive Equation card); this coefficient is equivalent to the shear modulus G in most cases, as described below.
Definitions of the input parameters are as follows:
{model_name} |
Name of the Lame Mu coefficient model. This parameter can have one of the following values: CONSTANT, POWER_LAW, CONTACT_LINE, SHEAR_HARDEN, EXPONENTIAL, DENSE_POWER_LAW, or USER. |
{float_list} |
One or more floating point numbers (<float1> through <floatn>) whose values are determined by the selection for {model_name}. These are identified in the discussion of each model. |
The details of each model option are given below:
All modulus values in these equations have the same units as Lame Mu, i.e., M/Lt2.
Examples#
The following is a sample card:
Lame MU = CONSTANT 1.
Technical Discussion#
Note that \(\mu\) and \(\lambda\), (see the Lame LAMBDA card) are related to the more often used Young’s Modulus and Poisson’s Ratio by the following standard expressions:
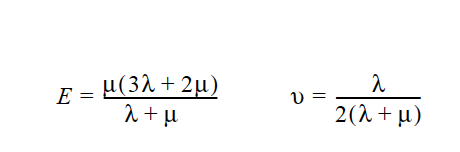
where E is the Young’s modulus and υ is Poisson’s ratio. A significant limiting case is approached as \(\nu\) approaches 0.5, in which case the solid becomes incompressible.
The POWER_LAW option could easily be adapted to a concentration measure, viz. made dependent on the concentration of some species (see EQ = species_bulk card). This can be done through the user option, and in fact in usr_lame_mu function of file user_mp.c in the Goma distribution has an example that is appropriate. Also note that all of these models are available for the elastoviscoplastic option on the Plasticity card, and for the real-solid in TOTAL_ALE mesh motion.
FAQs#
Important note that when one desires an incompressible solid through the use of INCOMP_PSTRAIN type models, by using an incompressible continuity equation in a LAGRANGIAN mesh region (see EQ = continuity), then the bulk modulus, or Lame Lambda expansion term is also added on. So to get a truly incompressible response, one must set the Lame LAMBDA coefficient to zero.
References#
Sackinger, P. A., Schunk, P. R. and Rao, R. R. 1995. “A Newton-Raphson Pseudo-Solid Domain Mapping Technique for Free and Moving Boundary Problems: A Finite Element Implementation”, J. Comp. Phys., 125 (1996) 83-103.
Scherer, G.W., 1992, “Recent Progress in Drying of Gels”, J. of Non-Crystalline Solids, 147&148, 363-374
GT-001.4: GOMA and SEAMS tutorial for new users, February 18, 2002, P. R. Schunk and D. A. Labreche
GT-019.1: Elastoviscoplastic (EVP) Constitutive Model in GOMA: Theory, Testing, and Tutorial, P. R. Schunk, A. Sun, S. Y. Tam (Imation Corp.) and K. S. Chen, January 11, 2001
GTM-027: Probing Plastic Deformation in Gelatin Films during Drying, M. Lu, S. Y. Tam, A. Sun, P. R. Schunk and C. J. Brinker, 2000
SAND96-2149: Drying in Deformable Partially-Saturated Porous Media: Sol-Gel Coatings, Cairncross, R. A., P. R. Schunk, K. S. Chen, S. S. Prakash, J. Samuel, A. J. Hurd and C. Brinker (September 1996)